What are supply chain metrics & KPIs?
A supply chain is the sequence of tasks that need to be undertaken in order to distribute a commodity. When a company needs to gauge the performance of its supply chain, it uses a range of different supply chain metrics & KPIs. Each key performance indicator provides a slightly different vision of one slice of the supply chain.
- What are supply chain metrics & KPIs?
- Making Use of Performance Metrics
- Features of a Functional Performance Metrics
- Some key characteristics of a useful performance metrics
- Comprehensible
- Easy to collect
- Quantitative
- It measures what’s important
- Leads to productive behaviour
- Three main categories of supply chain metrics & KPIs
- An Overview of KPIs for Supply Chain Management
- What are supply chain metrics & KPIs? What Does It Do?
- Essential Supply Chain metrics & KPIs You Can’t Do Without
- Inventory Turnover
- Perfect Order Rate
- Inventory Accuracy
- Shipment Time
- Return Reason
- Cash to Cash Cycle Time
- Warranty Costs as a Percentage of Sales
- Supply Chain Management and All that It Entails
- Choosing the Right Supply chain metrics & KPIs
- Conclusion
Making Use of Performance Metrics
For any company, the issue involves the need to prioritize the number of supply chain performance metrics to be used.
Many corporations use metrics that are easy to calculate. However, these indicators may not always present an accurate picture of how the supply chain is truly performing.
On the other hand, some companies also make use of a wide range of supply chain metrics and KPIs that the logistics department is told to adhere to. However, other parts of the supply chain might be adversely impacted as a result of this strict adherence to a range of predetermined metrics.
Features of a Functional Performance Metrics
Companies need to identify the key performance indicators that will help them with effective supply chain management, which will, in turn, enable the business to prosper. A good performance metric will also help management make savvy and well-informed business decisions.
Some key characteristics of a useful performance metrics
Comprehensible
A good metric is not overly technical. Ideally, it should be simple enough that it can be easily understood and interpreted by anyone who looks at it. How the metric is derived and what exactly it is measuring should be clear and easy to understand.
Easy to collect
Some performance metrics are complex, unwieldy, and hard to collect. Collecting these metrics might be time-consuming, which would force staff members to take time out from their jobs to prepare the metrics. Such an approach is counterproductive as it lowers the efficiency and overall productivity of the organization. Hence, complex and hard-to-collect metrics should be avoided whenever possible.
Quantitative
A supply chain performance metric must be expressed in objective terms, via a value that is quantitative. In other words, the metric must be derived from real and tangible data that is not in any way subjective or open to interpretation.
It measures what’s important
Some metrics can look complex and important. However, once the data has been analyzed, it is not hard to see that the relevance of the metric is, at best, tenuous. Hence, a key performance indicator on the basis of which important business decisions are made must be measuring data that is both important and highly relevant.
Leads to productive behaviour
A useful performance metric is one that promotes and facilitates productive behaviour. For instance, a metric that measures the number of orders processed during a given period would encourage the management to try and increase the speed of processing orders. On the other hand, a metric that measures the movements of workers in a warehouse might simply encourage the workers to enhance the frequency of their movements without performing any relevant or productive tasks.
Three main categories of supply chain metrics & KPIs
Most supply chain performance metrics fall within one of three main categories. These are:
Time
Time-based performance indicators are easy to calculate and understand. The time required to process an order, fulfil an order, or the number of on-time receipts and deliveries are some examples of this category of performance metrics.
Cost
In order to be profitable, a business needs to be fiscally efficient and have great cash flow. This is where cost metrics can come in useful, as they can help a company identify areas of fiscal inefficiency and make the required changes for greater profitability. Inventory carrying costs, which tell a business how much money is being spent to store items in a warehouse, is one of the popular cost-based metrics.
Quality
Key performance indicators that focus on quality are rare. However, they are vital for the purpose of improving customer satisfaction, which is something that every business needs. The quality of the products and services being sold must be improved constantly in order to keep pace with the expectations of the customers.
An Overview of KPIs for Supply Chain Management
A key performance indicator (KPI) is a quantifiable measure that is used to assess the success of an entity, or an organization. A KPI measures how well the entity being evaluated was able to meet the objectives for performance, and from that data, the assessment is derived.
Some of the must-have supply chain KPIs for effective management are inventory turnover, freight bill accuracy, days sales outstanding (DSO), perfect order rate, cash to cash cycle time, inventory accuracy, warranty costs as a percentage of sales, and delivery or shipment time.
The use of a KPI to improve performance by businesses is nothing new. However, to truly understand these metrics, we must first get an accurate picture of what exactly we are dealing with. You might ask, therefore, what is a KPI and how can it be of use to me?
What are supply chain metrics & KPIs? What Does It Do?
A key performance indicator, sometimes also known as a key success indicator, allow companies to self-evaluate their performance in certain key activities that may have to do with individual products, projects, or other sections of the workflow.
The progress that has been made towards the achievement of goals can be measured with the help of a KPI. Moreover, companies can also use KPIs to measure their performance against those of other businesses operating in the industry.
KPIs can vary greatly from one industry to the next, as the goals and workflows of companies in different industries can be very different from one another. Even different departments within the same company can have KPIs that are distinct from one another.
For instance, the sales department of a company might track KPIs such as pricing against competitors and client acquisition rates. On the other hand, the HR department would be more interested in metrics such as annualized voluntary turnover rate and employee satisfaction levels.
Hence, a KPI cannot be right or wrong. It can only be relevant and useful within a particular context. A KPI that makes sense for a particular project in a specific situation may prove to be completely irrelevant or useless in a different situation.
Other Aspects
Keeping that in mind, with the right KPIs, managers can get an accurate idea of how an enterprise is performing. This objective measurement tool will enable them to identify problems quickly and make adjustments. This is very important to match the accordance with the shifting business landscape.
With these KPIs, a complex system of a supply chain can be run smoothly with minimal glitches and disruptions. Read on to know more about the key supply chain KPIs used by e-commerce logistics and courier companies in India.
Essential Supply Chain metrics & KPIs You Can’t Do Without
Inventory Turnover
This key performance indicator measures exactly how efficiently an organization or company is able to move its inventory over a period of time. Inventory turnover is a metric that can help you gain a clearer understanding of supply chain efficiency as well as the buying practices of the organization. Moreover, this KPI will also help you accurately gauge the demand for one of your services or products.
In essence, this is a metric that shows how often a business is able to sell off its entire inventory over the course of a year. A quick movement of inventory lowers storage expenditure and also enables the company to sell its products at premium rates, instead of offering discounts to clear the stock at the end of the year.
Perfect Order Rate
For businesses operating in more than one sector or industry, this is an extremely important performance metric. The perfect order rate is essentially used to measure a company’s ability to complete the delivery of orders without any issues or incidents.
The number of times an order was delivered in a perfect and error-free manner, in terms of timeliness, delivery costs, and quality of the product delivered, and the ratio of such perfect orders to total orders reflects how efficient the organization is.
The higher the perfect order rate is, the more successful the business has been in ironing out issues such as inaccuracies, delays, inventory losses, and other types of possible damages. The perfect order rate is also directly correlated with rates of customer satisfaction and brand loyalty.
Inventory Accuracy
The numbers on your inventory management database should always match the products stored in your physical inventory. In retail businesses, however, there can often be a significant disparity between the two. According to the RFID Lab of Auburn University in Alabama, inventory accuracy in retail is 63 per cent on average.
This can lead to a rise in inventory and logistics costs as well as unexpected backorders. This is why inventory accuracy KPIs are so important in the retail sector, as they can help management regularly compare the physical inventory to the numbers shown on the database, thus minimizing inefficiencies by bridging the gap between the two.
Shipment Time
The delivery and shipment times are an essential performance metric for courier companies in India and around the world. This KPI is also widely used by the parcel and distribution businesses as well as shippers. Both on-time shipments and timely delivery are very important for the success of a company, especially in terms of e-commerce logistics, as the online retail industry is very dependent on timely and safe deliveries.
Meeting the expectations of the customers in terms of shipping times and delivery speed is very important for improving the rates of retention and loyalty. Hence, this metric should be tracked and measured regularly for an accurate picture of how well the business is serving its customers.
Return Reason
This metric is of great value for the supply chain management of an e-commerce company. Essentially, it provides an insight into the main reasons why customers are returning the items that they have ordered. This KPI is derived from data that is easy and inexpensive to collect, as customers can simply be asked to check a box online and mention the reason when they try to return an item that they purchased.
The data is then presented in a simple pie-chart format with different colours indicating the major or most common reasons for items being returned. This allows a business to assess its own weaknesses, analyze the quality of its supply chain and the critical areas within it, and make the improvements necessary to minimize returns and improve the quality of service being provided. This KPI, when analyzed and implemented properly, will lead to fewer returns, enhanced profits, and better cash flow.
Cash to Cash Cycle Time
This valuable KPI can give businesses a lot of key information about various parts of the supply chain. In essence, it is the difference in time between when a business pays its suppliers to purchase inventory and when it receives money from its customers in return for goods sold.
THEREFORE, this KPI can be used to estimate the amount of cash required to fund the day-to-day operations of the business, and hence, the overall financing requirements of the company.
This metric can help enhance the efficiency of a retail supply chain and reduce logistics costs. Being able to track and measure the average cash-to-cash cycle can also help companies notice any abnormal delays in payment.
Warranty Costs as a Percentage of Sales
The cost of providing a warranty for products should be calculated as a percentage of sales. This will help you minimize the costs incurred due to flaws in the quality control group. This KPI also allows companies to get a clear picture of the money spent on repairing and replacing units. Other than this it also helps in calculating the cost of a warranty compared to the total sales revenue.
This metric is important for gauging the success of a business, as warranty costs can seriously impact the bottom line. Hence, if the cost of repairing faulty products is too high, it could cause the business to lose profits and become unsustainable in the long run. So this metric should be scrupulously tracked and the required improvements should be made to ensure that warranty costs never run high enough to become unsustainable.
Supply Chain Management and All that It Entails
Supply chain management can be a complex and nuanced task, and by no means is it an exact science. Logistics teams and departments around the world are not only working overtime to increase the efficiency of their supply chains but also working to increase the profitability of their organization.
Complex interdependencies between various departments, teams, partner companies, and branches across international borders need to be managed and directed in order to maximize the efficiency of operations while minimizing costs.
In order to accomplish such a complex and colossal task, performance metrics and key performance indicators are needed so that the management team can get a bird’s-eye view of the operations so as to be able to make key decisions effectively. Metrics help us understand trends by studying and analyzing data and recognizing patterns.
All industries, including retail, IT, and sales, make use of these metrics. KPIs can measure anything from procurement, inventory, warehousing, and transportation to production, packaging, material handling, and customer service. Apart from these, there are many more areas for which KPIs can be used.
Hence, we can say that there are hundreds of metrics available to gauge the performance of supply chain management. For years now, businesses have been measuring KPIs for logistics. This is improving the operational efficiencies of different businesses.
The Standard supply chain metrics and KPIs
The ones that you need to use will depend on the particular requirements of your business. The priorities of your clients and customers will determine the KPIs that you need to go with. Generally, when dealing with supply chain management, you can expect to see the following set standards in regards to KPI.
- Cost as a Percentage of Sales
- DOT or Delivery on Time
- DIF or Delivery in Full
- DIFOT or Delivery in Full on Time
Regardless of the particularities of the business or company, these metrics are instrumental, simply because they’re universal.
The debt to equity ratio may or may not apply to a small, privately-owned retail or e-commerce logistics firm. But every business needs to please and retain customers. This will help them turn a profit. In order to do so, they must make high-quality, timely deliveries and keep track of their costs.
Choosing the Right Supply chain metrics & KPIs
Therefore, when thinking about KPIs and performance metrics, it is important not to get bogged down in tracking and analyzing too many intricate and obscure KPIs.
Rather, you should choose a few metrics which are easy to collect, and are relevant to your bottom line. It is important for your management team to realistically monitor, track, and react on a regular basis.
They need not be intricate or granular. Rather, they should effectively track the fundamental elements of supply chain performance.
Conclusion
Do you follow all the above supply chain metrics? Do let us know in the comment section below.
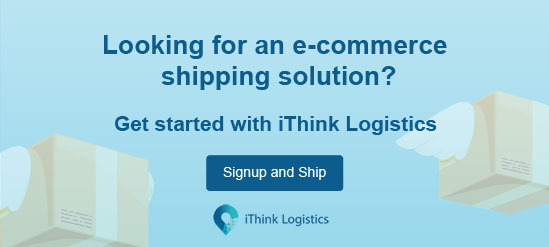